不織布の製造工程
不織布の製造工程には、フリース形成と繊維間結合の2工程があります。まず、フリースと呼ばれる繊維の集積層を形成し、次に繊維同士を結合させます。
不織布の素材・原料
天然繊維、合成繊維を初め、ガラス・金属・セラミックス・パルプ・炭素繊維など、およそ繊維と呼ばれるもののほとんどを原料にできます。一般的には、ポリエステルなどの合成繊維が多く使われます。
フリースを形成する主な方法
乾式法
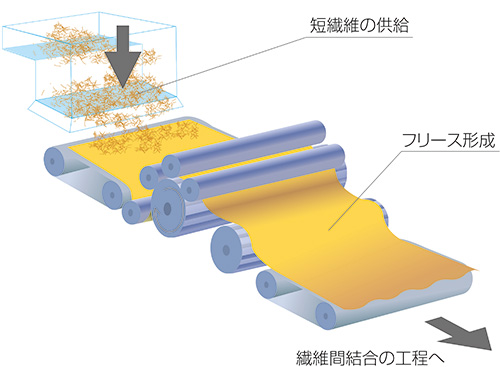
短繊維(15~100mm)を、カードと呼ばれる機械やエアレイと呼ばれる空気流で一定方向またはランダムに並べて形成する。
- 右図はカードと呼ばれる機械を用いた方法。
湿式法
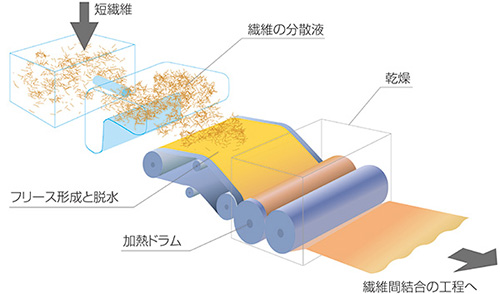
紙をつくる場合と同じように、ガラス繊維やパルプ原料のようなごく短い繊維(6mm以下)を水中に分散し網状のネット上にすき上げてフリースを形成する。
- 特長
- 厚さが均一で、※目付(めつけ)を自由に変えることができる。
- 主な用途
- ワイピングクロス、おしぼり、おむつ、フィルタ、ティーパック、特殊繊維シート(ガラス繊維、etc.)など。
- 目付(めつけ)とは単位面積あたりの質量のこと
スパンボンド法
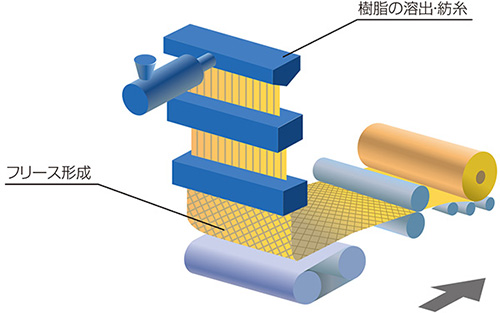
原料樹脂を溶融・紡糸させ得られる連続した長い繊維を直接集積してフリースを形成する。
- 特長
- 用途に合わせた設計ができる。連続した長い繊維で形成されているため引っ張り強度が強い。広幅、高速生産も可能。
- 主な用途
- おむつ、土木資材、建築用防水シート、フィルタ、芯地、カーペット基材、コーティング/ラミネート基材、包装資材など。
メルトブローン法
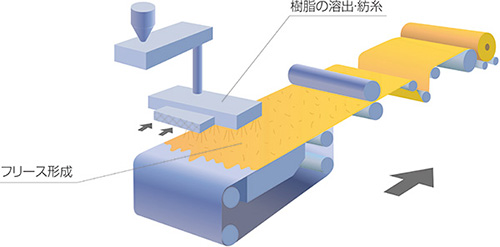
樹脂を溶融して紡糸ノズルの周囲から噴射する高温エアにより、繊維を細くしてシート状に集積します。
- 特長
- 樹脂から直接シート化できるので効率が良い。
風で延伸するので繊維径を細くできる(1~10μm)
乾式・湿式法では作れない細い繊維だけで構成される不織布を作ることができる。
- 主な用途
- ビル空調用フィルタ、キャビンエアフィルタ、OA機器用フィルタ、マスク、液体フィルタなど
フリースを結合させる主な方法
サーマルボンド法
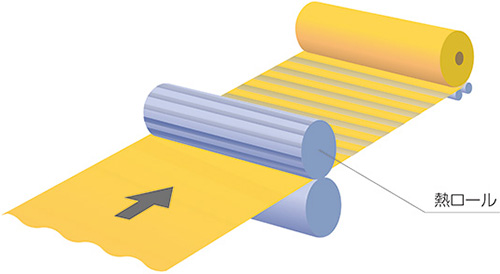
低融点の熱融着繊維を混合したフリースを、熱ロールの間を通して熱圧着する。または熱風を当て、繊維同士を接着させる。
- 特長
- 接着剤を使用しないためソフトな風合い。
- 主な用途
- おむつ、生理用ナプキン、特殊工業資材など。
ケミカルボンド法(含浸法)
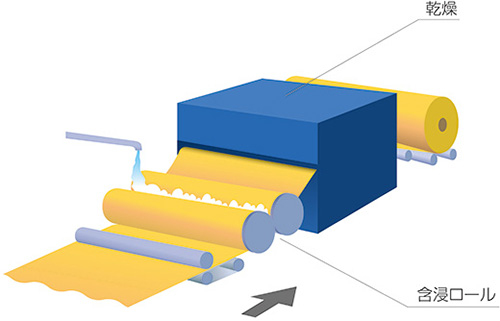
エマルジョン系の接着樹脂を含浸あるいはスプレーなどの方法でフリースに付着させ、加熱・乾燥させて繊維の交点を接着する。
- 特長
- 柔軟性とドレープ性に富む。
- 主な用途
- 芯地、コーティング用基材、カーペット基材、工業資材など。
ケミカルボンド法(スプレー法)
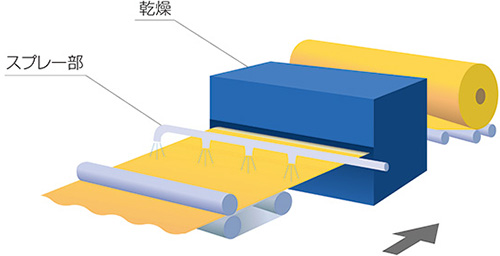
フリースにバインダの溶液をスプレーし、乾燥させてかさ高な状態で繊維間を結合します。
- 特長
- フリースを構成する繊維の交点だけを接着剤で固定できるので
かさ高く・ソフトな風合いの不織布を作ることができる。
- 主な用途
- 粗じんフィルタ、中わた、ブラジャーカップなど
ニードルパンチ法
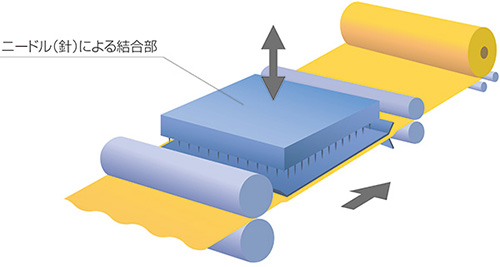
フリースを、高速で上下するニードル(針)で繰り返し突き刺し、ニードルに刻まれたバーブという突起により繊維を絡ませる。この方法だけで製品化したり、別の結合法と組み合わせて用いる。
- 特長
- バルク性に富み、繊維間のはく離がない。
- 主な用途
- 床材、フィルタ、コーティング基材、自動車用内装材、土木資材など。
水流絡合法
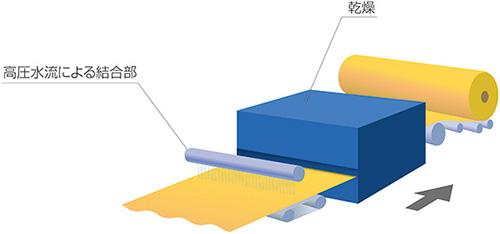
フリースに高圧の水流を柱状に噴射して繊維を絡ませる。
- 特長
- 柔軟でドレープ性に富み、毛羽立ちしない。
- 主な用途
- おむつ、医療資材、芯地、コーティング基材、ワイピングクロス、生活資材(掃除用、食品用、収納用)など。
一連の工程
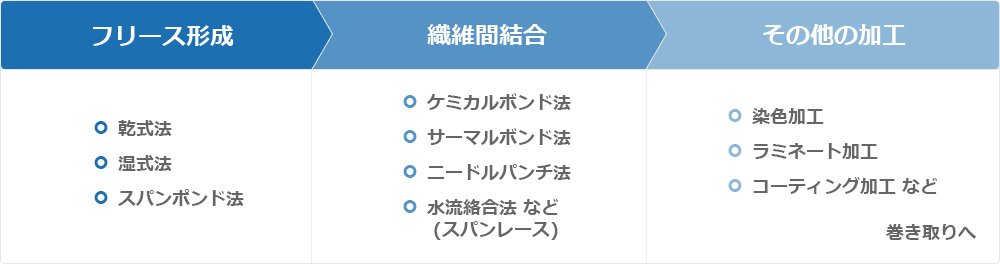